“Si yo me recibo, se viene el mundo abajo”, pensaba Juan D´Adamo antes de rendir su último examen universitario. “Y más o menos eso pasó”, bromeaba después de aprobarlo. Era el 22 de diciembre del 2001 y el eco de las movilizaciones del 19 y 20 todavía se escuchaba en los alrededores de la facultad de ingeniería.
Juan siempre supo que lo suyo era la investigación y la docencia, que eligió ingeniería en lugar de física o historia (sus materias preferidas en el Nacional Buenos Aires) cediendo al mandato paterno. Pero a la hora de abrirse paso en el ámbito laboral, no tenía dudas: su lugar en el mundo sería un laboratorio.
En el convulsionado principio de siglo, tardó un tiempo hasta conseguir una beca de investigación que lo pusiera en la carrera que añoraba. Por esos años un ministro de economía había osado mandar a los científicos a lavar los platos, como respuesta a sus reclamos por el escaso presupuesto que el Estado les asignaba. La ofensa caló hondo en Juan y sus compañeros y todavía la recuerdan, está flotando en el fondo de sus conciencias cuando presentan en sociedad el circuito de válvulas que desarrollaron para salvar vidas en medio de la pandemia.
¿Cómo fue el camino que los llevó a desarrollar este circuito?
JD: Nosotros estudiamos una materia de ingeniería mecánica que se llama dinámica de los fluidos, y si bien no es nuestra especialidad estudiar problemas de biomédica, nuestros conocimientos nos permitían reorientar la investigación que veníamos haciendo para aportar una solución, en un tiempo relativamente corto, a la crisis sanitaria derivada de la escasez de respiradores.
Empecemos por el principio: ¿qué es la dinámica de los fluidos?
JD: Es el estudio de cómo se mueven los fluidos, que son los gases o líquidos que están presentes en nuestra vida cotidiana. Están en el agua que circula en las cañerías de una ciudad y en el aire que atraviesa un avión en su vuelo. Lo que veníamos estudiando era cómo optimizar gastos de energía en la interacción de fluidos con sólidos. Una de las hipótesis se enfocaba en el rol de la flexibilidad de las estructuras. Por ejemplo, un generador eólico: si las palas son flexibles pueden capturar más energía. Entonces pensábamos cómo la flexibilidad podría dar mejores respuestas. Ese es el tema en el cual yo estaba trabajando hasta que nos embarcamos a diseñar el circuito.
¿Por qué eligieron un circuito de válvulas y no directamente diseñar un respirador?
JD: Los respiradores son aparatos complejos, llevaría meses su diseño porque hay que resolver problemas de electrónica y también de informática. Y el director del laboratorio, el Dr. Ing. Guillermo Artana, había visto que en Italia, cuando no daban abasto con los respiradores, algunos médicos duplicaban su uso poniéndoles una bifurcación con forma de T en la salida del aire para conectar a dos pacientes simultáneamente.
Esa solución tiene varios problemas: uno, que los dos pacientes pueden tener distintas necesidades de oxígeno. Frente a eso lo que hacían era agrupar pacientes que sean más o menos de contextura o problemática parecida y los ponían a respirar juntos. Pero tiene otro problema: la contaminación de un paciente hacia el otro.
Nosotros vimos que este problema era bien de dinámica de fluidos y que nuestro laboratorio podía aportar una solución. Tras una búsqueda bibliográfica encaminamos nuestro diseño en las primeras semanas de marzo. Con el paso de los días nos fuimos enterando que en otras partes del mundo (Bégica, Inglaterra, Estados Unidos) llegaban a soluciones similares.
Manos a la obra
El primer paso fue diseñar una válvula que permite regular la cantidad de aire que pasa por un tubo, evitando que se introduzcan contaminantes. Dos compañeros del equipo de Juan estuvieron a cargo de esa tarea. A esta válvula la bautizaron “Pinch”: es un dispositivo donde una manguera es aplastada por un pistón que se puede mover con una pequeña manivela.
El segundo paso era conseguir que cada paciente reciba la cantidad de oxígeno que necesita, controlando la presión, tanto de la entrada como de la salida de aire del pulmón. Otras válvulas se sumaron al dispositivo con esta función. La tercera cuestión era evitar que se contaminen las vías entre sí, para eso utilizaron válvulas unidireccionales, que solo permiten el flujo en una sola dirección.
Así llegaron al circuito que llamaron ACRA: Ampliación de la Capacidad de Respiradores Artificiales.
Trabajo interdisciplinario
El 18 de mayo el diario Clarín difundió la noticia en su suplemento Rural: “La Facultad de Ciencias Veterinarias impulsa un dispositivo que duplica el alcance de los respiradores.” Es que el trabajo conjunto con la Facultad de Veterinaria fue clave para que el invento que nació en Ingeniería llegara a buen puerto.
Habitualmente los desarrollos médicos antes de utilizarse en humanos se ponen a prueba en animales, y eso había que hacer con la válvula. “El Dr. Pablo Otero, de la cátedra de Anestesiología Veterinaria, le vio enseguida la utilidad a nuestro desarrollo y nos ayudó a mejorarlo. Nosotros teníamos un circuito funcional medio rústico y con él lo adaptamos para que un médico lo pueda utilizar con facilidad. Nos ayudó a pensar como lo haría un clínico, entender sus necesidades”, cuenta el Dr. Ing. Juan D ´Adamo.
También colaboró la carrera de Diseño Industrial de la FADU. “Ellos mejoraron aspectos prácticos de la maqueta que luego imprimimos en una impresora 3D”. Otras dos instituciones hicieron su aporte: “También tuvimos un ida y vuelta con investigadores de Santa Fe (del Centro de Investigación de Métodos Computacionales, que pertenece al Conicet) y de La Plata (de YPF Y-TEC). A ellos les pedimos realizar una simulación numérica del problema del aplastamiento de la manguera con un sólido: qué pasa con el aire que circula cuando la manguera está apretada.”
Cuando todas las variables estaban bajo control y el prototipo final terminado, la válvula se probó en cerdos con resultados satisfactorios. “Ahí los focos empezaron a caer sobre nosotros. Luego del artículo que publicó Clarín Rural se hizo una nueva prueba en animales que tuvo mucha difusión y fue seguida con gran interés en los hospitales.”
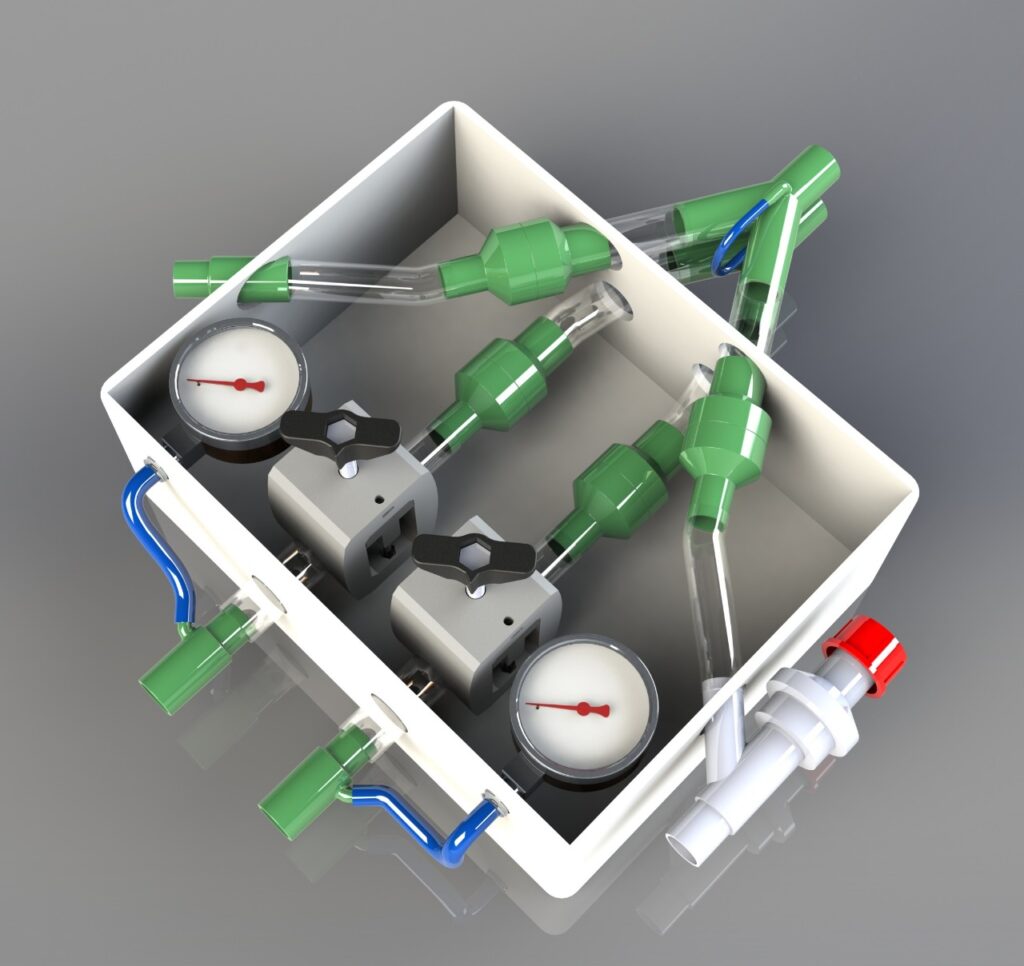
El último paso
Fabricar el circuito en el laboratorio tiene un costo de entre 200 y 300 dólares. Teniendo en cuenta que un respirador sale entre 10.000 y 15.000 dólares, el ACRA es un respaldo accesible para los hospitales en medio de una emergencia. Para producirlo a escala industrial, falta la aprobación de la ANMAT. La UBA hizo la presentación a principios de mayo ante ese organismo y, al cierre de esta nota, aún estaban a la espera de su respuesta.
Mientras tanto, desde el laboratorio de fluido dinámica de la facultad de Ingeniería están proveyendo a hospitales de la UBA los circuitos que fabrican en sus impresoras 3D. ♦